Berufswäsche und Textillogistik: Reaktionszeiten
Facility Management: Berufswäsche / Textillogistik » Strategie » Ausschreibung » Reaktionszeiten (zur Verhandlung)
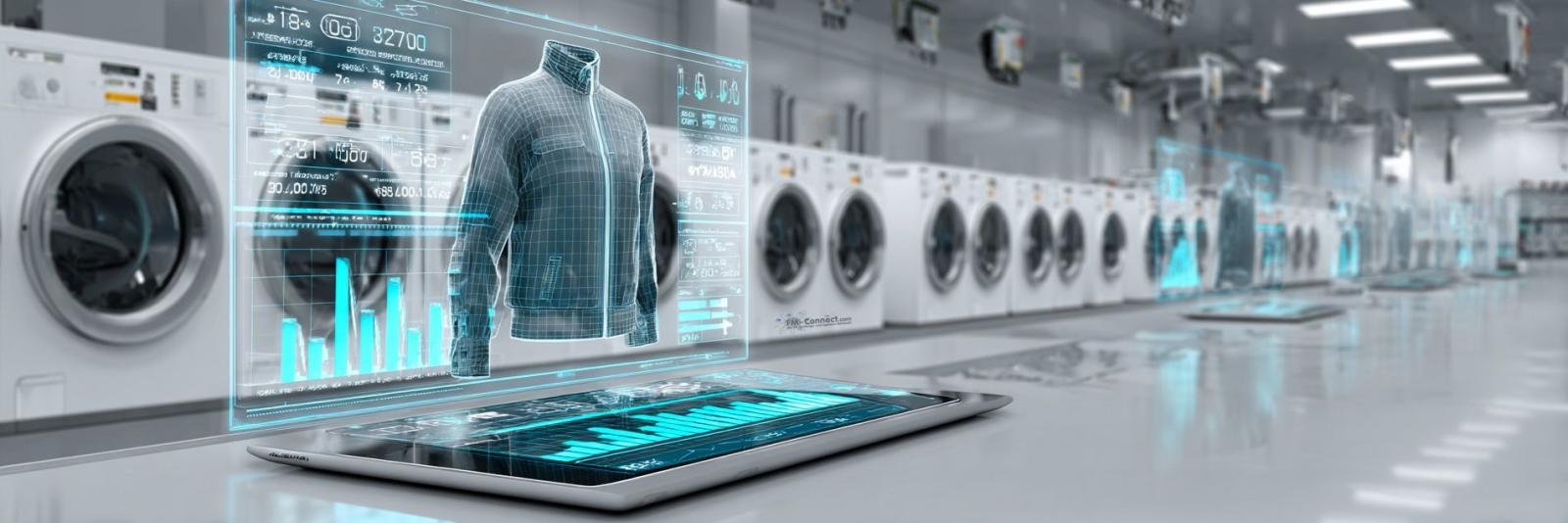
Reaktionszeitenmatrix für die Berufskleidungs- und Textillogistik (Mietwäsche)
In einem großen Industriebetrieb mit Mietwäsche-Versorgung ist es geschäftskritisch, dass benötigte Berufskleidung jederzeit in ausreichender Menge und einwandfreiem Zustand verfügbar ist. Reaktionszeiten beschreiben, wie schnell auf Ereignisse oder Anforderungen reagiert wird – sei es die Beschaffung neuer Kleidung, das Beheben eines technischen Defekts oder das Nachfüllen von Beständen. Kurze und verlässliche Reaktionszeiten, abgestuft nach Priorität, stellen sicher, dass Produktionsabläufe nicht durch fehlende Kleidung unterbrochen werden und dass Arbeitsschutzvorgaben stets erfüllt sind.
Es ist festzuhalten, dass die Versorgungssicherheit in der Berufskleidungs-Logistik durch ein Zusammenspiel aus präventiven Maßnahmen (Pufferbestände, Wartung), modernen Technologien (RFID-Tracking, automatische Ausgabesysteme) und klar definierten Prozessen/SLAs erreicht wird. Wie schnell reagiert der Dienstleister in kritischen Fällen? Welche Garantien gibt es vertraglich? Und welche Referenzwerte aus der Branche liegen vor? Mit einer gut durchdachten Reaktionszeitenmatrix als Teil des Servicekonzepts lässt sich die jederzeitige Verfügbarkeit von Berufskleidung sicherstellen und damit Ausfallrisiken und organisatorische Last für den Betrieb auf ein Minimum reduzieren.
Reaktionszeiten im Management von Berufswäsche
Geschäftsprozesse in der Mietwäsche-Logistik
Ein Großbetrieb muss diverse Geschäftsprozesse etablieren, um die kontinuierliche Versorgung mit Berufskleidung sicherzustellen.
Wichtige Prozesse sind unter anderem:
Beschaffung (Nachschub) : Die Bereitstellung neuer oder zusätzlicher Berufskleidung durch den Mietwäsche-Dienstleister. Hierzu zählt die Bestellung von Kleidung bei Bedarf sowie das Vorhalten eines Textilpools. Beispiel: Wenn neue Mitarbeiter eingekleidet werden müssen oder zusätzliche Schutzkleidung benötigt wird, muss der Dienstleister schnell für Nachschub sorgen. Durch festgelegte Umlaufmengen pro Mitarbeiter (typisch 3–5 Garnituren) und einen ausreichenden Puffer wird vorgesorgt. Dies stellt sicher, dass jederzeit genügend Kleidung im Umlauf ist und Neubeschaffungen im Normalfall planbar sind.
Lagerhaltung & Bestandsmanagement : Die Verwaltung der Lagerbestände an sauberer und getragener Kleidung. Dazu gehört das Auffüllen von Ausgabestationen und das Überwachen von Mindestbeständen. Beispiel: Moderne Systeme überwachen automatisch die Bestände und Nutzungsmuster, um Engpässe zu vermeiden. Sinkt der Vorrat unter definierte Schwellenwerte, erhält der Dienstleister automatisch eine Meldung und kann außerhalb des normalen Turnus nachliefern. Dieses proaktive Bestandsmanagement verhindert, dass Mitarbeiter vor leeren Schränken stehen. Gleichzeitig werden regelmäßige Inventuren (z. B. quartalsweise) durchgeführt, um Soll- und Ist-Bestände abzugleichen und Verluste aufzudecken.
Ausgabe : Die Bereitstellung sauberer Berufskleidung an die Mitarbeiter, in der Regel über Ausgabeautomaten oder Ausgabestellen. Beispiel: Im Idealfall kann jeder Mitarbeiter rund um die Uhr (24/7) saubere Kleidung entnehmen, z. B. aus einem RFID-gestützten Kleiderautomaten. Die Ausgabe erfolgt damit bedarfsgerecht und ohne Wartezeit. Wichtig ist, dass vor Schichtbeginn ausreichend frische Kleidung vorhanden ist (ein SLA kann z. B. einen spätesten Befüllzeitpunkt vor Schichtbeginn vorschreiben). Sollte ein Mitarbeiter keine passende Kleidung vorfinden (z. B. wegen unerwartetem Mehrbedarf), muss kurzfristig reagiert werden – etwa durch manuelles Öffnen des Automaten oder Bereitstellen von Ersatzkleidung aus einem Pufferbestand.
Rücknahme : Die Entgegennahme getragener, schmutziger Berufskleidung zur Weiterverarbeitung. Mitarbeiter geben getragene Teile typischerweise in dafür vorgesehenen Rückwurf-Systemen oder Wäschecontainern ab. Beispiel: In vielen Betrieben sind Ausgabe und Rücknahme gekoppelt, etwa durch Schränke mit Rückgabeklappe. Die zurückgegebene Wäsche wird per RFID erfasst und dem Mitarbeiterkonto zugeordnet. Dieser Prozess läuft kontinuierlich, damit verschmutzte Kleidung umgehend dem Waschprozess zugeführt wird. Bei besonders kontaminierter oder beschädigter Kleidung greifen Sonderprozesse: kontaminierte PSA wird sofort separiert und nach speziellen Vorgaben entsorgt oder gereinigt, beschädigte Kleidung wird zur Reparatur ausgesteuert.
Reinigung : Das Waschen und Aufbereiten der getragenen Berufskleidung in der Industriewäscherei. Hier gelten strenge Hygiene- und Pflegevorschriften, vor allem bei Persönlicher Schutzausrüstung (PSA), damit die Schutzfunktionen erhalten bleiben. Beispiel: Der Dienstleister sorgt für einen schnellen Wäscheumlauf, damit saubere Kleidung rechtzeitig zurückkommt. In der Praxis bedeutet dies, dass Wäsche planmäßig z. B. innerhalb 2–3 Tagen wieder bereitgestellt wird (im Regelprozess). Bei dringendem Bedarf kann auch schneller gewaschen werden – in Notfällen binnen 24 Stunden oder am selben Tag, ggf. mit Sonderschichten. Wichtig ist auch die Nachweisdokumentation, dass z. B. desinfizierende Wäscheverfahren korrekt durchgeführt wurden (gerade im Gesundheits- oder Lebensmittelbereich).
Reparatur : Das Ausbessern defekter Kleidungsstücke (z. B. kaputte Nähte, Reißverschlüsse oder abgenutzte Reflexstreifen). Beispiel: Kleinere Schäden werden vom Service während des normalen Zyklus behoben, ohne dass der Träger es merkt. Ein Reparaturservice stellt sicher, dass defekte Teile entweder sofort repariert oder durch ein Ersatzstück ausgetauscht werden. PSA-Kleidung erfordert hierbei besondere Sorgfalt, damit die Schutzwirkung erhalten bleibt. Defekte mit Einfluss auf die Sicherheit (z. B. Riss in flammhemmender Kleidung) haben oberste Priorität – hier wird oft sofortiger Austausch vorgenommen und das defekte Teil getrennt behandelt. Nicht sicherheitsrelevante Mängel (z. B. lose Knöpfe) können im normalen Turnus behoben werden.
Austausch : Der planmäßige oder außerplanmäßige Austausch von Kleidungsstücken. Dies umfasst den Größentausch (wenn Mitarbeiter eine andere Größe benötigen), den Saisonaustausch (z. B. Winterjacken im Herbst) oder den Austausch verschlissener Kleidung. Beispiel: Bei Neueinstellungen wird die Erstausstattung zügig bereitgestellt – oft werden für neue Mitarbeiter oder Praktikanten ausreichende Mengen an Kleidung in gängigen Größen vorgehalten, damit sie sofort etwas zum Anziehen haben. Individuelle, personalisierte Kleidung (etwa mit Namensschild) wird meist innerhalb weniger Tage nachgeliefert (ein Vertrag kann z. B. vorsehen, dass spätestens 3 Werktage nach Anprobe die Kleidung bereitsteht). Routineaustausch (etwa Ersatz abgenutzter Teile) erfolgt im regulären Lieferzyklus, während dringende Austauschbedarfe (z. B. stark verschmutzte Kleidung, die sofort ersetzt werden muss) außerplanmäßig bedient werden.
Entsorgung : Das Aussortieren und fachgerechte Entsorgen nicht mehr nutzbarer Kleidung. Verschlissene oder beschädigte Teile, die nicht mehr repariert werden können, werden aus dem Umlauf genommen. Beispiel: PSA mit abgelaufener Schutzwirkung (z. B. Chemikalienschutz mit Ablaufdatum) oder irreparabel defekte Kleidung wird umgehend aussondiert. Kritische Fälle (z. B. kontaminierte Einweg-Overalls nach Chemieunfall) werden sofort entsorgt. Ansonsten wird in regelmäßigen Abständen gesammelt entsorgt, oft gekoppelt mit der Lieferung neuer Ersatzkleidung. Der Prozess ist so gestaltet, dass entsorgte Kleidung rechtzeitig ersetzt wird, damit die Umlaufmenge konstant bleibt.
Neben den Prozessen sind verschiedene technische Systeme und Hilfsmittel essentiell, um die Versorgung effizient und zuverlässig zu gestalten:
RFID-Systeme und Textilkennzeichnung : Jedes Kleidungsstück ist in der Regel mit einem eindeutigen Transponder/Chip (RFID) oder Barcode ausgestattet, um es individuell zu identifizieren. Dies ermöglicht das automatische Tracking aller Bewegungen (Ausgabe, Rückgabe, Waschzyklus) und hilft, Verluste zu minimieren. Beispiel: Füllt ein Mitarbeiter ein Teil in den Rückgabeschacht ein, registriert der RFID-Scanner sofort die Rückgabe. Beim Entnehmen aus dem Automat wird die Entnahme personalisiert verbucht. Reaktionsrelevanz: Wenn das RFID-System oder die Kennzeichnung ausfällt, verliert man die Bestandsübersicht. Daher sind hohe Verfügbarkeit und Redundanzen wichtig. In der Praxis werden RFID-Leser zentral überwacht; bei Störungen gibt es häufig mobile Ersatz-Lesestationen als Backup. Fällt z. B. ein Scanner aus, kann der Dienstleister oft per Fernwartung oder mit einem Austauschgerät innerhalb kurzer Zeit reagieren. Auch das Nachpatchen verlorener oder unlesbarer Transponder gehört dazu (in der Wäscherei werden defekte Chips i. d. R. sofort ersetzt).
Automatische Ausgabesysteme (Kleidungsausgabe-Automaten) : Schrank- oder Automatenlösungen, oft RFID-gestützt, aus denen Mitarbeiter ihre Kleidung selbstständig entnehmen und schmutzige wieder einwerfen können. Diese Systeme ermöglichen 24/7-Selbstbedienung und entlasten Personal. Beispiel: Ein Ausgabeschrank meldet in Echtzeit seinen Füllstand und eventuelle Störungen an die Zentrale. Reaktionsrelevanz: Bei technischen Problemen (z. B. Automat defekt oder Netzwerk ausgefallen) muss der Dienstleister schnell reagieren. Übliche SLAs fordern z. B. eine Reaktionszeit von maximal 24 Stunden bei Automatenausfall. In kritischen Fällen (Automat komplett außer Betrieb, Betrieb steht sonst ohne Kleidung da) werden sofort Notfallmaßnahmen eingeleitet: Remote-Diagnose, Entsenden eines Technikers, manuelles Notöffnen des Schrankes etc. Vertraglich kann z. B. festgelegt sein, dass innerhalb von 2 Stunden ein Techniker auf den Weg geschickt wird, wenn ein 24/7-Ausgabeautomat ausfällt. Kleinere Störungen (z. B. ein klemmendes Fach) werden oft bei der nächsten planmäßigen Befüllung behoben, sofern sie die Ausgabe nicht wesentlich beeinträchtigen. Wichtig ist außerdem ein Fallback: Viele Verträge verlangen einen Fallback-Prozess bei Automatenausfall, etwa manuelle Ausgabe durch einen Servicefahrer oder einen mobilen Ersatz-Schrank.
Waschtechnik und Finish : Die industriellen Waschmaschinen, Trockner, Mangel und Finishing-Anlagen in der Wäscherei, die für die Aufbereitung der Kleidung sorgen. Diese Anlagen sind auf hohe Durchsatzmengen ausgelegt und oft in vollautomatische Prozessstraßen eingebunden. Reaktionsrelevanz: Ein Ausfall kritischer Waschtechnik kann die termingerechte Rücklieferung gefährden. Deshalb haben große Textilservice-Betriebe meist Redundanzen (mehrere Maschinen, Ausweichkapazitäten) und Wartungsverträge. Beispiel: Fällt eine Haupt-Waschstraße aus, wird entweder die Wäsche auf andere Maschinen verteilt oder – falls nötig – in eine nahegelegene Partnerwäscherei transportiert. Die Reaktionszeit für die Reparatur wichtiger Anlagen liegt meist im Stundenbereich (sofortige Technikeralarmierung, Ersatzteilbeschaffung über Nacht). Kleinere Störungen oder Kapazitätsengpässe können oft intern kompensiert werden, sodass der Kunde davon nichts merkt. Zudem werden regelmäßige Wartungen außerhalb der Stoßzeiten durchgeführt, um überraschende Ausfälle zu minimieren.
Logistiksoftware und Tracking-Systeme : Zentrale IT-Systeme, welche alle Bewegungen der Kleidungsstücke protokollieren (Warenwirtschaft, Inventarverwaltung, Nutzerkontingente) und oft ein Web-Portal für den Kunden bieten. Beispiel: Das System erfasst jede Entnahme und Rückgabe in Echtzeit und zeigt dem Facility Manager an, welche Bestände vor Ort sind. Reaktionsrelevanz: Bei einem Ausfall der Software oder von Schnittstellen (z. B. zum RFID-System) muss schnell gehandelt werden, da sonst z. B. Entnahmen nicht registriert und Bestände nicht korrekt nachgeführt werden. Übliche Vereinbarungen sehen vor, dass Service-Hotlines oder IT-Support verfügbar sind, um Probleme sofort anzugehen (oft via Remote-Zugriff). Beispielsweise könnten SLAs hier eine erste Reaktion innerhalb weniger Stunden vorsehen und die Wiederherstellung wichtiger Systemfunktionen innerhalb eines Arbeitstags. In der Zwischenzeit wird auf Notfallprozesse umgeschaltet (z. B. manuelle Dokumentation der Entnahmen), damit die Kleiderausgabe weitergehen kann.
Fahrzeug- und Transporttechnik : Die Transportmittel (LKW, Transporter, ggf. interne Fördertechnik), mit denen saubere Kleidung geliefert und Schmutzwäsche abgeholt wird. Beispiel: Der Textilservice richtet feste Liefertouren ein, oft im festen Rhythmus (z. B. 2–3 Mal pro Woche) oder bei großem Betrieb sogar täglich. Die Fahrzeuge sind teils mit speziellen Vorrichtungen (Rollcontainer, Schrankaufbauten) ausgestattet, um einen schnellen Umschlag vor Ort zu ermöglichen. Reaktionsrelevanz: Wenn ein Lieferfahrzeug ausfällt (Panne, Unfall), muss trotzdem die Lieferung pünktlich erfolgen – Top-Anbieter halten dazu Ersatzfahrzeuge und Fahrer bereit. Bei kritischen Lieferungen (z. B. morgens vor Schichtbeginn) werden bei Störungen umgehend Ersatztransporte organisiert, um die vereinbarte Lieferzeit einzuhalten. Kleinere Verzögerungen werden kommuniziert und durch beschleunigte Entladung oder Wochenendfahrten ausgeglichen. In Ausnahmefällen – etwa bei außerplanmäßigem Sofortbedarf – können binnen kürzester Zeit (teils innerhalb 4 Stunden) Sonderfahrten erfolgen. Dieser Extremfall greift z. B. bei Notfällen oder unvorhersehbaren Verbrauchsspitzen (etwa Pandemien oder Unfällen), wo laut Vertrag zusätzliche Mietwäsche sehr kurzfristig geliefert werden muss, notfalls auch nachts oder am Wochenende.
Prioritäten und abgestufte Reaktionszeiten
Nicht jedes Ereignis erfordert die gleiche Reaktionsgeschwindigkeit. In der Praxis werden Prioritätsstufen definiert, um Ressourcen effizient einzusetzen und dennoch kritische Situationen unverzüglich zu bewältigen.
Üblich sind vier Stufen:
Kritisch : Höchste Priorität. Ereignisse, die unmittelbar die Sicherheit oder den Produktionsbetrieb gefährden, z. B. Ausfall der Kleiderausgabe insgesamt (kein Mitarbeiter kann sich einkleiden), akuter Mangel an PSA oder ein gravierender Hygienevorfall. Reaktion: Sofortige Maßnahmen, umgehend oder innerhalb weniger Stunden. Ein Techniker oder Servicefahrer wird unverzüglich alarmiert, ggf. innerhalb 2 Stunden vor Ort. Es wird häufig eine 24/7-Bereitschaft vorgehalten (Notfallnummer, Bereitschaftsdienst), um auch außerhalb der Geschäftszeiten zu reagieren. Beispiele: Totalausfall eines Ausgabeautomaten, Großunfall mit plötzlich hohem Wäschebedarf – hier gilt es, sofort zu handeln (siehe Matrix unten).
Hoch : Hohe Priorität. Wichtige Störungen oder Bedarfe, die zwar den Betrieb beeinträchtigen, aber nicht unmittelbar stilllegen. Beispielsweise Teilausfälle (ein Automatenteil defekt, aber andere Fächer funktionieren noch) oder Fehlmengen, die in Kürze kritisch werden könnten. Reaktion: Zeitnahe Bearbeitung, typischerweise innerhalb eines Arbeitstages (24 Stunden) oder gemäß SLA-Vorgabe. Beispielsweise kann ein SLA festlegen, dass bei Automatenproblemen innerhalb 24h eine Lösung erfolgt. Auch bedeutende Reklamationen (z. B. falsche Größen in einer Lieferung für mehrere Mitarbeiter) fallen in diese Kategorie – man erwartet schnelle Korrektur, aber der Betrieb läuft eingeschränkt weiter.
Mittel : Mittlere Priorität. Normale Betriebsfälle, die kurzfristig keinen größeren Schaden anrichten. Dazu zählen die meisten Standardprozesse: reguläre Nachlieferungen, geplante Größenwechsel, Reparaturen ohne Eile. Reaktion: Im Rahmen des regulären Turnus oder binnen weniger Tage. Oft werden Reaktionszeiten von z. B. 1 Werktag für Rückmeldung und 5 Werktagen für die Lösung vereinbart – ein Indikator, dass es sich um keinen Notfall handelt. Beispiel: Ein einzelnes Kleidungsstück fehlt in der Lieferung; hier reicht es, bis zur nächsten planmäßigen Lieferung (z. B. in 2–3 Tagen) nachzusteuern. Der Mitarbeiter hat evtl. genug Ersatz im Spind (durch das 3-Satz-System), sodass kein akuter Handlungsdruck besteht.
Niedrig : Geringste Priorität. Fälle, die ohne Eile behandelt werden können und meist im Zuge der nächsten Routinearbeiten erledigt werden. Dies umfasst etwa Routineaustausch wegen Verschleiß (der Träger kann das Teil bis dahin weiter nutzen), geplante Entsorgungen, kleinere Schönheitsreparaturen oder allgemeine Prozessoptimierungen. Reaktion: Im normalen Geschäftsablauf, z. B. zur nächsten Wartung oder Inventur, oft innerhalb einiger Wochen. Beispiel: Aussonderung einer alten Kollektion zum Quartalsende – dies wird gesammelt und muss nicht ad hoc erfolgen.
Diese Priorisierung stellt sicher, dass kritische Engpässe mit maximaler Dringlichkeit behoben werden, während weniger dringliche Themen effizient gebündelt werden können. Bei der Definition der Zeiten werden branchenspezifische Anforderungen berücksichtigt – z. B. gelten in Krankenhäusern oder Chemiebetrieben mit PSA strengere Maßstäbe an die Reaktionszeit (weil hier Sicherheit und Gesundheit unmittelbar abhängen), wohingegen in einem Verwaltungsgebäude die Dringlichkeit niedriger sein mag.
Reaktionszeitenmatrix: Geschäftsprozesse und Technik
Die folgende Matrix fasst typische Reaktionszeiten für die wichtigsten Prozesse und technischen Komponenten der Berufskleidungs-Logistik zusammen, jeweils abgestuft nach Kritikalität. Hinweis: Konkrete Werte können je nach Dienstleister, Branchenanforderung und SLA variieren. Die angegebenen Zeiten orientieren sich an Best Practices in der Mietwäsche-Branche und beispielhaften SLA-Vorgaben aus der Industrie.
Geschäftsprozesse (Serviceabläufe)
Prozess | Kritisch (z. B. Ausfall, Gefahr) | Hoch (dringend, störend) | Mittel (normaler Bedarf) | Niedrig (planbar, gering) |
---|---|---|---|---|
Beschaffung (Nachschub neuer Kleidung) | Sofortige Bereitstellung, z. B. aus Notvorrat oder Expresslieferung noch am gleichen Tag (innerh. Stunden). In Katastrophenfällen Lieferungen binnen 4h (vertraglich vereinbart). | Innerhalb 1 Tages: z. B. nächstmögliche Belieferung über Nacht oder am Folgetag bei dringendem Mehrbedarf. | Binnen 2–5 Werktagen: im normalen Bestellzyklus oder zur nächsten planmäßigen Lieferung (gewöhnlicher Nachschub). | Im regulären Zyklus: z. B. Bündelung mit nächster planmäßiger Beschaffung, keine Eile (einige Wochen Vorlauf bei Vorratsplanung). |
Lagerhaltung (Bestandssteuerung) | Unverzügliche Reaktion bei drohendem Bestandsnullstand: Alarmierung bei Unterschreiten Mindestbestand, Nachlieferung noch am gleichen Tag außerhalb der Reihe. | Innerhalb 24h: beschleunztes Auffüllen vor dem nächsten Schichtbeginn, falls Bestand knapp wird (z. B. Zusatzlieferung am Abend). | Routine-Zyklus: Nachfüllung laut Turnus (z. B. wöchentlich). Schwund und kleine Fehlmengen werden bis zur nächsten Lieferung toleriert, da Puffer vorhanden sind. | Periodische Auffüllung: Lagerbestände werden planmäßig geprüft (z. B. wöchentlich), Anpassungen bei Überbestand/Unterbestand im nächsten Rhythmus. Niedrige Priorität, solange Soll-Puffer greift. |
Ausgabe (Verteilung an Mitarbeiter) | Sofortmaßnahmen: Bei Ausfall der Ausgabe (Automat defekt, System down) sofort manuelle Notausgabe einleiten – z. B. Automat manuell öffnen, Ersatzschlüssel nutzen. Kein Mitarbeiter darf unversorgt zur Arbeit gehen. Techniker innerhalb 2h vor Ort bei Automatenausfall; ggf. mobiler Ersatzschrank noch am selben Tag. | Sehr zeitnah, max. innerhalb < 24h: Bei teilweisem Engpass (einzelne Größen vergriffen) Ausweichlösung bis zum nächsten Arbeitstag – z. B. Kleider aus benachbartem Standort holen oder Schichtleiter verteilt Reservekleidung. SLA-Beispiel: Automatenstörung innerhalb 24h behoben. | Schnellstmöglich im Normalbetrieb: Ausgabe ist i. d. R. permanent möglich (24/7 Automat). Kleinere Probleme (z. B. ein Fach geht nicht auf) werden bei nächster Service-Runde (1–3 Tage) behoben. Mitarbeiter können meist auf andere Fächer/Größen ausweichen. | Periodische Auffüllung: Lagerbestände werden planmäßig geprüft (z. B. wöchentlich), Anpassungen bei Überbestand/Unterbestand im nächsten Rhythmus. Niedrige Priorität, solange Soll-Puffer greift. |
Prozess | Kritisch (z. B. Ausfall, Gefahr) | Hoch (dringend, störend) | Mittel (normaler Bedarf) | Niedrig (planbar, gering) |
---|---|---|---|---|
Rücknahme (Schmutzwäsche-Erfassung) | Sofortbearbeitung besonderer Fälle: Stark kontaminierte oder gefährliche Schmutzwäsche wird umgehend separat behandelt (sofortiger Abtransport oder Sonderwäschelauf noch am selben Tag). | Binnen 24h: Falls Rücknahmesystem überfüllt oder defekt ist – innerhalb eines Tages leeren/tauschen, um Hygiene zu wahren. Dringende Reklamationen (z. B. falsch sortierte Schmutzwäsche) werden bis zum nächsten Tag bereinigt. | Standard-Rückführung: Schmutzwäsche wird gemäß vereinbartem Turnus abgeholt (z. B. mehrmals wöchentlich). Rückgaben fließen unmittelbar in den nächsten Waschzyklus ein (typ. 2–3 Tage Umlaufzeit). | Geplante Abläufe: Langfristige Rückläufe (z. B. Saisonartikel am Saisonende gesammelt zurück) erfolgen nach Absprache, ohne Eile. Keine akute Maßnahme nötig, solange die laufende Wäscheversorgung nicht beeinträchtigt ist. |
Reinigung (Wäscheaufbereitung) | Expressreinigung: Für dringend benötigte Teile (z. B. einzige verfügbare PSA eines Mitarbeiters) Sofortwäsche oder binnen 12 Stunden fertig gewaschen und geliefert. Notfalls Einsatz einer Sonderschicht oder Nacht-/Wochenendarbeit. | Beschleunigte Reinigung, z. B. innerhalb 24 Stunden fertig: Priorisierte Behandlung wichtiger Kleidungsstücke außer der Reihe (z. B. Uniformen für einen ungeplanten Einsatz am nächsten Tag). | Regulärer Waschzyklus: Wäsche wird laut Standardprozess gereinigt und binnen 2–3 Werktagen wieder bereitgestellt (übliche Laufzeit in Mietwäsche). Das 3-Satz-System stellt sicher, dass diese Dauer überbrückt wird. | Verlängerte Bearbeitung: Bei wenig genutzten Artikeln oder größeren zeitlichen Puffern (z. B. saisonale Garderobe) kann die Reinigung im erweiterten Zeitfenster erfolgen (z. B. bei geringer Auslastung später in der Woche). |
Reparatur (Ausbessern defekter Teile) | Ad-hoc-Ersatz: Bei sicherheitsrelevanten Schäden (PSA-Defekt) sofort Austausch des Kleidungsstücks – Mitarbeiter erhält umgehend Ersatz, Reparatur erfolgt nachrangig. Reaktionszeit für Ersatz oft < 1 Tag (teilweise sofort vom Fahrer gebracht). | Schnelle Reparatur: Wichtig, aber nicht sicherheitskritisch – z. B. kaputter Reißverschluss an Arbeitsjacke. Reparatur bzw. Tausch innerhalb 1–3 Tagen, meist bis zur nächsten planmäßigen Lieferung. | Im normalen Zyklus: Kleinere Mängel (loser Knopf, leichte Naht) werden bei nächster Wäsche automatisch erkannt und behoben; üblich innerhalb 1 Woche. Der Mitarbeiter kann das Teil bis dahin meist noch tragen oder hat Wechselkleidung. | Bündelung bei Gelegenheit: Minimale Mängel oder optische Reparaturen (z. B. ausgebleichter Namensaufnäher) werden gesammelt und in größeren Intervallen behoben (z. B. quartalsweise Austausch aller abgenutzten Embleme). |
Austausch (Größenwechsel, Kollektion, verschlissene Kleidung) | Soforttausch bei Bedarf: Passt eine Größe absolut nicht oder ist ein Teil unbenutzbar, erhält der Mitarbeiter noch am gleichen Tag ein passendes Ersatzstück (aus Vorrat vor Ort oder Expresszustellung). | Zeitnahe Umrüstung: Dringende Austausche (z. B. mehrere MA benötigen Winterjacken wegen Kälteeinbruch) innerhalb 2 Arbeitstage. Auch Kollektionstausch mit hoher Priorität (z. B. gesetzl. neue PSA-Norm) wird in wenigen Tagen umgesetzt. | Planmäßiger Austausch: Routine-Wechsel von Größen (nach Anprobe), Kollektionen oder altersbedingter Ersatz erfolgt innerhalb einiger Wochen nach Anmeldung. Z.B. neue Mitarbeiter sind spätestens 3 Werktage nach Anprobe vollständig ausgestattet (typisch vertraglich geregelt). | Langfristige Erneuerung: Nicht dringende Wechsel (z. B. Design-Update der Firmenkleidung) im Rahmen geplanter Projekte (mehrere Monate Vorlauf). Verschlissene Artikel werden gesammelt und zum Ende ihres Lebenszyklus ersetzt, ohne Eile. |
Entsorgung (Aussortieren unbrauchbarer Teile) | Sofortentfernung: Gefährliche oder hoch kontaminierte Kleidung, die nicht mehr genutzt werden darf, wird sofort aus dem Umlauf entfernt (z. B. in Sicherheitsbehälter) und umgehend entsorgt. Ersatz wird parallel beschafft (siehe Beschaffung kritisch). | Rasche Entsorgung: Deutliche Schäden oder PSA mit erloschener Schutzwirkung werden innerhalb weniger Tage ausgesondert, um Fehlverwendung zu vermeiden. Ggf. schneller Ersatzlieferung binnen 1 Woche. | Planmäßiger Austausch: Routine-Wechsel von Größen (nach Anprobe), Kollektionen oder altersbedingter Ersatz erfolgt innerhalb einiger Wochen nach Anmeldung. Z.B. neue Mitarbeiter sind spätestens 3 Werktage nach Anprobe vollständig ausgestattet (typisch vertraglich geregelt). | Geplante Ausscheidung: Größere Entsorgungsaktionen (z. B. Austausch einer ganzen Kollektion am Vertragsende) werden langfristig geplant und ohne Zeitdruck durchgeführt. |
Technische Komponenten (Infrastruktur & Ausrüstung)
Technik/Komponente | Kritisch (Totalausfall) | Hoch (starke Beeintr.) | Mittel (Teil-Störung) | Niedrig (Wartung/Opt.) |
---|---|---|---|---|
RFID-System / Kennzeichnung | Systemausfall: Bei komplettem Ausfall der RFID-Erfassung oder wenn keine IDs mehr ausgelesen werden können – sofortiger Wechsel in Notbetrieb. Beispielsweise Einsatz einer mobilen Lesestation vor Ort noch am gleichen Tag als Backup. IT-Support unverzüglich zur Fehlerbehebung (Remote oder vor Ort). | Erhebliche Störung: (z. B. viele Chips werden nicht erkannt) – innerhalb 24h müssen Gegenmaßnahmen erfolgen: Technikertermin am nächsten Tag, Ersatzlesegerät, manuelles Verbuchen als Übergang. | Minore Störung: (Einzelne Ausfälle, z. B. defekte Transponder bei einigen Kleidungsstücken) – Behebung im Rahmen des normalen Prozesslaufs, z. B. innerhalb 1 Woche: Defekte RFID-Tags werden in der Wäscherei ausgetauscht, Software-Patches beim nächsten Service-Update eingespielt. | Wartung & Update: Geplante Software-Updates oder Inventuren der RFID-Datenbank werden mit Vorlauf angekündigt und außerhalb der Stoßzeiten durchgeführt (z. B. nachts oder am Wochenende). Kein akuter Zeitdruck, solange das System stabil läuft. |
Automat/Ausgabestation | Totalausfall: Kompletter Ausfall der Kleiderausgabe (kein Automat verfügbar) – unverzüglich Notfallplan aktivieren: manuelle Ausgabe durch Servicepersonal oder Öffnen des Schranks zur Selbstbedienung. Techniker kommt sofort (<2h). Reparatur oder Austausch des Automaten i. d. R. innerh. 24h (vertraglich oft garantiert), ggf. provisorischer Ersatzschrank. | Schwerwiegende Störung: (Automat funktioniert, aber z. B. mehrere Fächer defekt oder Kartenleser ausgefallen) – spätestens am nächsten Werktag vor Ort reparieren. Bis dahin teilausweichender Betrieb (andere Fächer nutzbar). Nachfüllung ggf. außerplanmäßig, um Engpass auszugleichen. | Leichte Störung: (z. B. einzelnes Fach klemmt, Displayfehler) – innerhalb einiger Tage behoben, meist bei der nächsten planmäßigen Wartung oder Befüllfahrt (1–3 Werktage). Einfluss auf Ausgabe gering (Mitarbeiter nutzen Alternativen), daher moderat dringlich. | Präventive Wartung: Regelmäßige Inspektion des Automaten (z. B. jährlich) und Software-Updates werden geplant durchgeführt. Ausfallzeiten werden dabei vorher angekündigt (z. B. Wartungsfenster nach Schichtende), sodass keine akute Störung entsteht. |
Waschtechnik (Waschstraße, Trockner, etc.) | Kritischer Anlagenausfall: Ein zentrales Gerät (z. B. Haupt-Waschstraße) fällt aus und gefährdet fristgerechte Lieferungen – sofortiger Notfallplan: Techniker umgehend alarmieren, ggf. innerhalb Stunden vor Ort. Falls Reparatur länger dauert, Wäsche noch am selben Tag in anderes Werk umlenken oder Schichtbetrieb erhöhen, um Verzögerungen zu vermeiden. | Größerer Ausfall: (z. B. ein Teil der Kapazität fehlt) – Reaktion binnen 24h: Reparatur am nächsten Tag abgeschlossen oder Ersatzmaschine in Betrieb. Lieferzeiten werden eng überwacht, ggf. priorisieren welche Chargen zuerst gewaschen werden. | Kapazitätsminderung: (z. B. eine Maschine von mehreren fällt aus, aber Reserve vorhanden) – Reparatur innerhalb weniger Tage, da der Betrieb weiterlaufen kann. Der Ausfall wird in der Zwischenzeit durch Redundanz abgefedert (keine merkliche Wirkung für Kunden). | Präventive Wartung: Regelmäßige Inspektion des Automaten (z. B. jährlich) und Software-Updates werden geplant durchgeführt. Ausfallzeiten werden dabei vorher angekündigt (z. B. Wartungsfenster nach Schichtende), sodass keine akute Störung entsteht. |
Logistiksoftware (Management-System, Portal) | System down: Totalausfall der zentralen Software (keine Datenerfassung möglich) – umgehender IT-Einsatz. Innerhalb weniger Stunden muss zumindest ein Notbetrieb laufen (z. B. Offline-Backup, manuelle Erfassung), damit der Überblick gewahrt bleibt. Kritische Funktionen (Ausgabeautorisierung, Bestandsanzeige) werden falls möglich sofort überbrückt. | Schwerer Fehler: (z. B. falsche Bestandsanzeigen, viele User können nicht zugreifen) – Fehlerbehebung innerhalb 1 Tages durch Software-Update oder Zurücksetzen auf Backup. Bis dahin manuelle Workarounds (z. B. Kommunikation der Bestände per Telefon/E-Mail) an Kunde. | Teilfehler: (Ein Modul ausgefallen, z. B. Reporting oder ein Scanner sync nicht) – Fix innerhalb weniger Tage durch regulären IT-Support-Ticket. Keine unmittelbare Auswirkung auf Kernprozess, aber sollte zeitnah gelöst werden um volle Funktion zu gewährleisten. | Präventive Wartung: Regelmäßige Inspektion des Automaten (z. B. jährlich) und Software-Updates werden geplant durchgeführt. Ausfallzeiten werden dabei vorher angekündigt (z. B. Wartungsfenster nach Schichtende), sodass keine akute Störung entsteht. |
Fahrzeug-/Transporttechnik | Lieferung in Gefahr: Ein vorgesehenes Lieferfahrzeug fällt kurz vor der Auslieferung aus – sofort Ersatzfahrzeug einsetzen, um Lieferung pünktlich zuzustellen. Notfall-Hotline informiert sofort den Ersatzfahrer. In dringenden Fällen (z. B. PSA-Lieferung vor Schichtstart) kann auch ein Kurier in <2h beauftragt werden. | Lieferprobleme: (z. B. Fahrzeugpanne auf Tour) – Umdisponierung innerhalb von Stunden: nächster verfügbarer Wagen übernimmt Tour, Information an Kunden über Verspätung. Lieferung soll noch am selben Tag erfolgen, ggf. mit kleiner Verzögerung. | Geringe Beeinträchtigung: (leichte Verzögerung oder Änderung der Route) – Lösung innerhalb 1–2 Tagen: z. B. Ausfall eines Fahrzeugs führt dazu, dass Lieferungen um einen Tag verschoben werden, falls beim Kunden genügend Pufferwäsche vorhanden ist. | Geplante Fahrzeugwartung: Defekte an Fahrzeugen, die die Tour nicht gefährden (z. B. Klima ausgefallen), werden bei nächster Gelegenheit behoben. Regelmäßige Inspektionen der Flotte sind langfristig terminiert, ohne Einfluss auf Liefertermine. |
Legende: Kritisch = höchste Priorität (Notfall), Hoch = hohe Priorität (stark störend), Mittel = mittlere Priorität (normaler Servicefall), Niedrig = niedrige Priorität (planbar). In der Matrix genannte Zeiten (Stunden, Tage) sind branchenübliche Richtwerte. Konkrete vertragliche SLAs können hiervon abweichen, sollten aber in ähnlichen Größenordnungen liegen.
Zur Gewährleistung der zuverlässigen Kleidungsvorhaltung haben sich in der Praxis verschiedene Best Practices etabliert:
Mehrsatz-System und Pufferbestände: Jedem Mitarbeiter werden mehrere Kleidersätze zugeteilt (typisch 3–5 Sätze). So ist immer mindestens ein Satz verfügbar, selbst wenn einer in der Wäsche und einer in Nutzung ist. Zusätzlich halten Dienstleister oft Poolbestände an Reservekleidung bereit, um Spitzenbedarfe oder Ausfälle abzufedern. In Ausschreibungen wird etwa gefordert, dass jederzeit ausreichend Textilien vorhanden sind und feste Umlaufmengen gewährleistet werden.
Automatisierte Bestandsüberwachung: Moderne Textilmanagementsysteme verfolgen in Echtzeit, wie viele Stücke von jeder Sorte im Umlauf und vor Ort sind. Sobald Bestände unter definierte Schwellen sinken oder untypische Verbrauchsspitzen auftreten, alarmiert das System proaktiv den Dienstleister. Dadurch können Nachlieferungen oder Nachproduktionen eingeleitet werden, bevor ein Engpass beim Mitarbeiter entsteht. Diese datengetriebene Vorgehensweise ist ein wichtiger Erfolgsfaktor, um Reaktionszeiten kurz zu halten.
Service Level Agreements (SLAs): In Verträgen zwischen Kunde und Textildienstleister werden klare Kennzahlen zur Leistung festgelegt. Typische SLA-Parameter in der Berufskleidungs-Logistik sind z. B. Lieferpünktlichkeit (z. B. >99%), Automatenverfügbarkeit (z. B. >98%), maximale Reaktionszeit bei Störungen und maximale Behebungsdauer. Beispiele: „Reaktionszeit bei Automatendefekt: max. 24h“, „Erstmeldung bei Reklamationen innerhalb 1 Werktag, Lösung innerhalb 5 Werktagen“. Bei anspruchsvollen Kunden findet man auch Vorgaben wie „Reaktionszeit 4 Stunden, Wiederherstellungsbeginn innerhalb 12 Stunden“ für bestimmte Störungsfälle. Solche SLAs geben dem Kunden Sicherheit und dem Dienstleister klare Ziele. Werden sie verletzt, greifen oft Vertragsstrafen (Pönalen).
Notfallkonzepte: Für kritische Situationen werden vorab Notfallpläne vereinbart. Dazu gehört eine 24/7-Notfall-Hotline und definierte Eskalationsketten: Wer informiert wen, wenn z. B. um 3 Uhr morgens ein Automat ausfällt? Gute Dienstleister haben mobile Ersatztechnik (Ersatzautomaten, Lesegeräte) griffbereit und definierte Prozesse, z. B. dass im Wachdienst ein Zweitschlüssel für manuelles Öffnen hinterlegt wird. Auch Zusatzlieferungen bei Katastrophen/Pandemie sind bedacht: Ein Beispiel aus einem Vertrag fordert bei außergewöhnlichen Umständen Lieferung zusätzlicher Mietwäsche binnen 4 Stunden auf Anforderung. Solche Vorkehrungen gewährleisten, dass auch in Ausnahmesituationen die Kleidungsvorsorge aufrechterhalten bleibt.
Transparenz und Reporting: Ein weiterer Best Practice ist die Bereitstellung von Online-Portalen und regelmäßigen Reports. Der Kunde (Facility-/Textillogistik-Manager) kann darüber Bestände, Entnahmen, laufende Reklamationen und Leistungskennzahlen jederzeit einsehen. Monatliche KPI-Berichte (z. B. Reklamationsquote, Reaktionszeiten, Wäschedurchlaufzeiten) schaffen Vertrauen und ermöglichen es, Trends früh zu erkennen. Bei Abweichungen von Zielwerten wird gemeinsam analysiert und der Prozess ggf. angepasst – so werden kontinuierlich Verbesserungen erzielt.
Qualitätssicherung und Schulung: Um die Servicelevel zu halten, investieren führende Anbieter in Qualitätsmanagement (z. B. ISO 9001 Zertifizierung) und regelmäßige Schulungen. Mitarbeiter in der Wäscherei und Logistik werden für den richtigen Umgang mit PSA geschult, technische Teams üben den schnellen Austausch von Automatenmodulen, und es gibt klar dokumentierte Prozesshandbücher für alle Abläufe. Dies stellt sicher, dass im Ernstfall jeder Handgriff sitzt und die vereinbarten Reaktionszeiten eingehalten werden können.